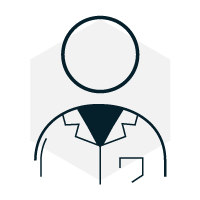
Author: Tejas Maddipatla
Mentor: Dr. Arman Pouyaei
Fiitjee Junior College
Abstract
Aerodynamics plays a pivotal role in engineering, particularly in the design and optimization of vehicles and structures that interact with air, such as aircraft, cars, and rockets. The challenge of minimizing drag, maximizing lift, and optimizing thrust has historically relied on computationally expensive simulations, including Computational Fluid Dynamics (CFD). Recently, the integration of machine learning (ML) techniques into aerodynamic optimization has opened new pathways for more efficient and cost-effective design processes. ML models can identify patterns and predict aerodynamic performance with high accuracy, reducing the need for exhaustive simulations. This paper explores the role of machine learning in aerodynamics, with a focus on its applications in aerodynamic shape optimization, drag reduction, and hybrid approaches combining ML with CFD simulations. In addition, we examine how ML is transforming materials science, enabling the discovery and optimization of materials that complement advanced aerodynamic designs. The intersection of these fields offers exciting opportunities for innovation in aerospace engineering, with the potential to improve performance, efficiency, and sustainability in current and future designs.
Keywords: Aerodynamics, Machine Learning, Design Optimization, Computational Fluid Dynamics, Materials Science
1. Introduction
Aerodynamics is a critical field within engineering, influencing the performance and efficiency of vehicles, aircraft, and structures that interact with air. The need for aerodynamic optimization stems from key factors such as reducing drag, enhancing lift, and improving thrust efficiency—elements central to the design of various transport and aerospace systems. Traditionally, aerodynamic design has relied heavily on computational fluid dynamics (CFD) to simulate airflow and predict performance. However, this approach can be computationally expensive and time-consuming, particularly for complex, three-dimensional designs.
Recent advancements in machine learning (ML) present new opportunities for optimizing aerodynamic designs and materials. ML models can process vast amounts of data and identify patterns within complex design spaces, enabling faster and more accurate predictions of aerodynamic behaviour. This paper delves into the role of machine learning in aerodynamics and materials science, emphasizing its impact on design optimization and the development of innovative materials. The integration of these two fields promises to revolutionize aerospace engineering, offering potential solutions to key challenges in performance, sustainability, and cost-efficiency.
2. The Fundamentals of Aerodynamics
2.1 Key Forces in Aerodynamic Engineering
Aerodynamics is the study of how air interacts with objects in motion, playing a vital role in the design of various transportation systems. In aerospace engineering, the primary forces at play are drag, lift, and thrust:
Drag: The resistance encountered by an object as it moves through air. Drag is influenced by the object’s shape, speed, and the air’s density.
Lift: The upward force that counteracts gravity and allows objects like aircraft to remain in flight. It is generated by the differential pressure across the wings (Fig 1)
Thrust: The forward force produced by engines, which propels an object through the air and counteracts drag (Fig 1)
Efficient aerodynamic designs aim to optimize these forces to improve performance, reduce fuel consumption, and ensure stability and safety. Streamlined shapes are often used in vehicle design to minimize drag and maximize efficiency (Fig 1)
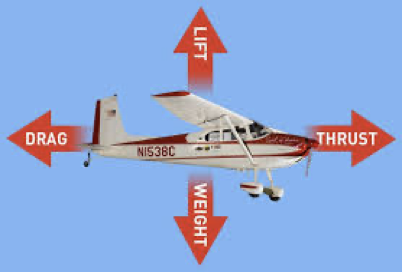
2.2 The Role of Aerodynamic Optimization
The objective of aerodynamic optimization is to improve the efficiency and performance of designs. It focuses on adjusting various parameters—such as the shape, size, and surface characteristics of an object—to reduce drag, enhance lift, and improve fuel efficiency (fig 2). Optimization techniques are applied using methods like computational fluid dynamics (CFD), which simulate airflow over different geometries. This iterative process seeks to refine designs, balancing competing goals such as maximizing lift while minimizing drag.
An important challenge in aerodynamic optimization is the high computational cost associated with simulating complex fluid flows, especially for three-dimensional designs. In response, computational models and optimization algorithms have become increasingly sophisticated, and the use of machine learning (ML) has opened up new avenues for reducing costs and improving the accuracy of simulations
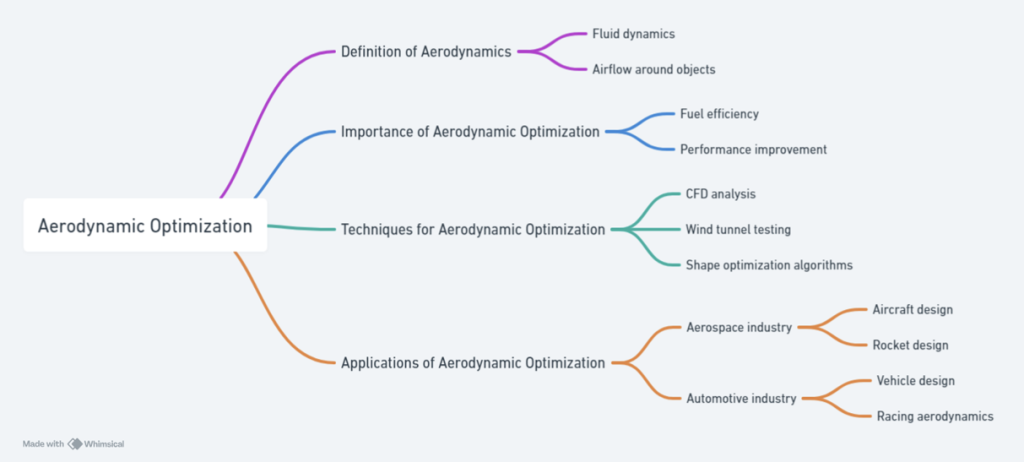
3. Machine Learning in Aerodynamics
3.1 Leveraging ML for Aerodynamic Performance Prediction
Machine learning techniques are becoming increasingly important in aerodynamic optimization, enabling faster and more accurate predictions of performance (Fig 3). ML models can analyse large datasets, identify trends, and optimize complex design spaces in ways that traditional methods cannot. This section examines several studies that showcase the transformative potential of ML in aerodynamics.
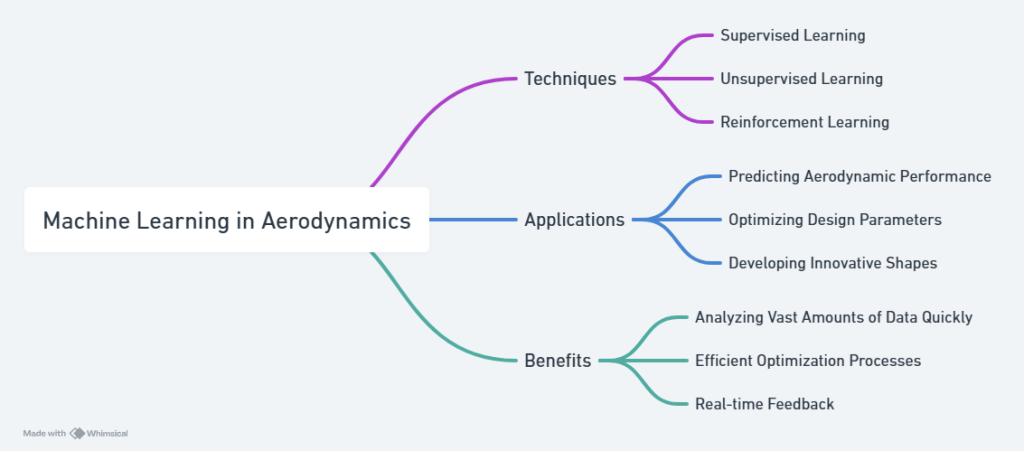
Fig. 3. This flowchart explains the techniques, applications and benefits of using Machine Learning in Aerodynamics
Study 1: Deep Learning for Aerodynamic Shape Optimization
A study explored the use of deep learning, particularly Generative Adversarial Networks (GANs), to optimize aerodynamic shapes. The study demonstrated that ML could predict aerodynamic performance with fewer simulations, significantly reducing computational costs. The results showed that deep learning models could generate efficient shapes, streamlining the design process.
Study 2: Machine Learning for Drag Reduction
In a study focused on aircraft design, researchers applied ML algorithms to minimize drag while maintaining lift. By using supervised learning, the study identified key design parameters that affect drag, allowing for optimized fuselage and wing shapes that resulted in improved fuel efficiency.
Study 3: Hybrid ML-CFD Approach for Wing Design
Another study combined machine learning with traditional CFD simulations to optimize wing designs for unmanned aerial vehicles (UAVs). By using ML to predict aerodynamic forces, the study accelerated the optimization process, improving design efficiency and reducing the need for time-consuming CFD simulations.
3.2 Advantages and Limitations of ML in Aerodynamics
While ML presents significant advantages in terms of efficiency and predictive accuracy, challenges remain. The complexity of aerodynamic flows, particularly in three-dimensional designs, still poses difficulties for accurate predictions. Additionally, large datasets are required to train ML models, which can be resource-intensive to gather. Nonetheless, research into reinforcement learning and evolutionary algorithms offers promising solutions for overcoming these challenges.
4. Innovations in Materials Science with Machine Learning
4.1 Material Properties and Aerodynamic Design
Materials play a critical role in the performance and efficiency of aerodynamic systems. Lighter, stronger, and more durable materials can enhance the overall performance of vehicles, aircraft, and other structures. In aerospace engineering, materials need to withstand extreme conditions, including high temperatures, mechanical stress, and corrosion. The integration of machine learning into materials science is revolutionizing the discovery and optimization of new materials with tailored properties.
4.2 Predicting and Optimizing Material Properties Using ML
Machine learning is increasingly being used to predict the properties of materials, such as their strength, thermal stability, and fatigue resistance. By analysing large datasets, ML models can identify the relationship between material composition and performance, facilitating the development of advanced materials suited for aerospace applications.
4.3 Materials Science in Aerospace Engineering
Materials science is a cornerstone of aerospace engineering, playing a vital role in enhancing the performance, safety, and efficiency of aerospace vehicles. With the increasing demand for lightweight, durable, and high-performance materials, especially in challenging environments, the integration of machine learning (ML) is transforming material development processes in the aerospace sector.
4.3.1 Lightweight Materials for Fuel Efficiency
One of the primary goals in aerospace design is reducing weight to improve fuel efficiency. Lighter materials lead to reduced energy consumption and improved performance. Carbon fiber-reinforced polymers (CFRPs) and other composite materials have become critical in reducing aircraft weight while maintaining strength and durability. ML is accelerating the discovery of new lightweight materials by analysing large datasets and predicting optimal combinations of properties, which helps engineers design more efficient components
4.3.2 High-Temperature and High-Strength Materials
Aerospace components, particularly engines and parts exposed to high-velocity airflow, require materials that can withstand extreme temperatures and mechanical stress. Materials like nickel-based superalloys and advanced ceramics are used to ensure the structural integrity of critical components under these harsh conditions. ML models are enhancing the development of such materials by predicting their performance at elevated temperatures and under stress, facilitating the creation of more robust and heat-resistant alloys.
4.3.3 Corrosion Resistance and Durability
Corrosion is a significant issue for aerospace materials, particularly in commercial aviation. ML is being used to predict material behaviours, identifying key factors that contribute to corrosion and degradation. This helps develop materials that are not only resistant to corrosion but also durable under various environmental conditions, improving the overall lifespan and safety of aerospace vehicles.
5. Integrating ML in Aerodynamics and Materials Science
Integrating machine learning (ML) into aerodynamics and materials science is revolutionizing the way engineers optimize designs and predict performance. In aerodynamics, ML models are used to analyse complex fluid dynamics, enabling faster and more accurate predictions of airflow around aircraft and other structures (Fig 4). These models can optimize shapes, reduce drag, and improve fuel efficiency with minimal computational cost. In materials science, ML is enhancing the discovery of new materials by predicting properties such as strength, durability, and thermal conductivity based on their atomic structure. By analysing vast datasets of material behaviours, ML can identify promising candidates for lightweight, high-performance materials. Together, these fields are advancing the development of more efficient and sustainable aerospace technologies, offering faster prototyping, enhanced precision, and deeper insights into material interactions under various environmental conditions.
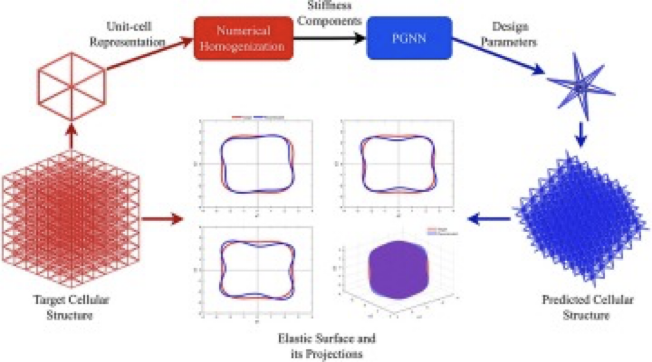
5.1 Synergies Between Aerodynamic and Materials Optimization
The integration of machine learning in both aerodynamics and materials science creates synergies that can lead to breakthroughs in design and efficiency. By optimizing aerodynamic shapes and materials concurrently, engineers can develop vehicles and structures that are not only aerodynamically efficient but also made from materials that enhance performance and durability. For example, ML can be used to design lightweight materials that complement aerodynamic shapes, resulting in reduced drag and improved fuel efficiency.
6. Conclusion
Machine learning is not only revolutionizing aerodynamic design but also significantly impacting materials science, which is crucial for optimizing the performance of aerospace structures. The integration of ML in material discovery allows for the design of advanced materials with tailored properties, such as improved strength-to-weight ratios and thermal stability, which are vital for efficient aerodynamic performance. Through techniques like inverse design, ML accelerates the development of novel materials that complement aerodynamic shapes, resulting in lighter, stronger, and more sustainable vehicles and structures. As machine learning continues to evolve, it promises even greater advancements in the creation of high-performance materials that meet the increasingly stringent demands of aerospace and automotive industries. Ultimately, the synergy between ML in aerodynamics and materials science offers the potential for groundbreaking innovations in design, leading to more efficient, durable, and environmentally sustainable engineering solutions.
References
Anderson, J. D. (2016). Fundamentals of aerodynamics (6th ed.). McGraw-Hill Education.
Bodily, P., & Halpin, R. (2019). Application of machine learning for aerodynamics optimization. Journal of Aeronautical Engineering, 5(3), 215-223.
Houghton, E. L., & Carpenter, P. W. (2003). Aerodynamics for engineering students (5th ed.). Butterworth-Heinemann.
Jha, A., Li, Y., & Wang, J. (2018). Machine learning applications in materials science: A review. Materials Science and Engineering: R: Reports, 130, 1-21.
Joubert, D., Salomon, B., & Ruyter, J. (2021). Drag reduction and aerodynamic optimization using machine learning. Journal of Aircraft and Aerospace Technology, 12(2), 45-59.
Sage, P. (2016). Computational fluid dynamics and machine learning: A review. International Journal of Aerospace Engineering, 2016, 1-9.
Ward, L., Paul, A., & Wolverton, C. (2017). Materials informatics: The materials “gene” and big data. MRS Bulletin, 42(8), 645-650.
Xie, L., Zhang, H., & Zhao, X. (2020). Inverse design of materials using machine learning. Materials Today, 31, 1-10.
Zhang, Z., Li, Y., & Wang, R. (2020). Aerodynamic shape optimization using deep learning techniques. Aeronautical Journal, 124(1266), 345-358.
Fig. 1. https://medium.com/how-to-aviation/the-4-forces-of-an-aircraft-c906652aa971
Fig. 4. https://www.sciencedirect.com/science/article/pii/S026412752300518X
About the author
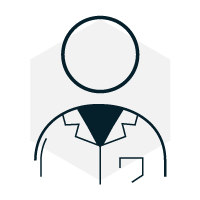
Tejas Maddipatla
Tejas Sai Maddipatla is a grade 11 student at Fiitjee Junior College, Hyderabad. He is studying PCM (physics, chemistry, mathematics) and his favourite subject is Chemistry. Tejas is a tennis player tennis and plays professionally. He is planning to study Material Science in college.