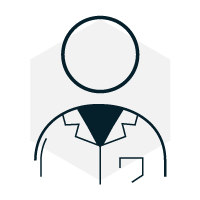
Author: Preston Wang
Mentor: Dr. Ben Yu, PhD
Tesoro High School
Introduction
Climate change remains a pressing global challenge, with 2023 marking record highs in global greenhouse gas levels, temperatures, and sea levels (Provisional State of the Global Climate 2023, 2023). The frequency and scale of extreme weather events continue to rise, as evidenced by the United States’ record of $92.9 billion in damage from such events in 2023 (2023: A Historic Year of U.S. Billion-Dollar Weather and Climate Disasters, 2023). In addition to the environmental impacts of climate change, the impact of climate change to mental health has been a significant topic in scientific inquiry and medical research recently (Hwong et al., 2022). According to the American Psychological Association, 68% of American adults are experiencing some level of climate anxiety; while 47% of the younger generation of 18-34 are experiencing such anxiety that affects their daily lives (APA, 2020). The worsening climate conditions is a great fear and cause of distress for many populations, showing the importance of a solution. The urgency to improve climate change has become a critical challenge for human existence. However, despite efforts to promote initiatives to mitigate climate change impacts, the United Nations’ 2023 report highlighted insufficient progress in slowing climate change (New Analysis of National Climate Plans: Insufficient Progress Made, COP28 Must Set Stage for Immediate Action | UNFCCC, 2020). As climate change keeps intensifying, climate anxiety is only going to get worse, making the need to find a solution to climate change a crucial goal for the world.
A promising solution lies in the circular economy, which emphasizes sustainable resource usage to minimize waste through repurposing, recycling, and redesigning. However, according to the 2021 Circularity Gap Report, only 8.6% of the global market currently adheres to this model (CGR 2021, 2021). Efforts are underway worldwide to adopt circular practices in many countries and agencies, reducing waste that contributes to carbon dioxide and methane emissions. One area of focus is landfills, which account for 170 million metric tons of carbon dioxide emissions and 17.7% of total U.S. methane emissions (Food Waste and Its Links to Greenhouse Gases and Climate Change, 2024). Methane is far more potent than carbon dioxide as its effect on warming is 72 times greater than carbon dioxide (Basic Information about Landfill Gas | US EPA, 2016).
Another area of focus is agricultural activities which also contribute to greenhouse gas emissions through food waste, unharvested productions, and slow sales (USDA ERS – Food Loss: Why Food Stays on the Farm or off the Market, 2017). Approximately 30% of global food loss and waste are attributed to agricultural production and harvesting (USDA ERS – Food Loss: Why Food Stays on the Farm or off the Market, 2017). Thus, reducing the greenhouse gas emissions from landfills and farms play a significant factor in climate change. Tackling this issue must entail repurposing one of the most frequently thrown away products, like banana peels, as they are one of the most consumed fruits globally with 135 million tons produced globally in 2022 (Bananas: Production Volume Worldwide 2022 | Statista, 2022) and produces a great amount of waste in landfills. Up to 40% of a banana’s mass is discarded as peel waste (Mohamed et al., 2023), and an additional 30 to 40% of harvested bananas at farms are discarded due to quality standards, leading to substantial agricultural waste (Punongbayan et al., 2021). In addition, bananas are mostly only eaten at their peak ripeness stage, which leads to large waste. Thus, the disposal of bananas presents a significant challenge.
Historically, banana peels have been utilized for livestock feed, fertilizer, human consumption, and by-product production, including water purification and bioplastics (Mohamed et al., 2023). Emerging research suggests that banana peels have fire retardant properties, making them a promising alternative in building materials, a sector responsible for a considerable share of carbon dioxide emissions and producing 39% of the world’s carbon dioxide (United Nations and the International Energy Agency). Banana peels have thus become a suitable solution to improve circular economy integration in the building sector (Antonella Violano & Cannaviello, 2023).
Banana peels have lignocellulose, tannic acid, phosphorus, sugar, and carbohydrates, but their chemical compositions and concentrations vary across ripening stages, influencing their fire retardant properties. For instance, ripe banana peels exhibit higher sugar, phosphorus, and lignin content, while unripe banana peels contain more carbohydrates, cellulose, and tannic acids (Hikal et al., 2022). Carbohydrates and phosphorus contribute to high char yields, creating insulation layers that push flames away (Liu et al., 2007). Tannic acids exhibit fire retardancy by releasing carbon dioxide at 200°C with a high char yield (Price et al., 2021) when exposed to flames. Carbon dioxide is a common chemical used in fire extinguishers which works to cool down the area and remove the oxygen (Types of Extinguishers | Ohio University, 2024). Similarly to the traditional carbon sugar snake experiment, sugar carbonates with the carbon dioxide which aids in carbon foaming to intensify. The intensification of carbon foam creates more physical barriers to delay heat transfer (Sugar and Salts Create Sponge for Capturing Carbon Dioxide – Materials Today, 2022). Lignocellulose, comprising cellulose, hemicellulose, and lignin, is known for its fire retardant capabilities through mechanical strength and a high char yield. A study indicated that lignin with phosphorus base increases in its fire retardancy value (Chollet et al., 2019).
Despite extensive research on banana peel bio-composites, the impact of ripening-induced chemical changes on their thermal properties remains largely unexplored. Understanding these dynamics is crucial for integrating banana peel waste into the circular economy effectively, considering the varying ripening stages encountered throughout the supply chain.
Literature Review
Prototypes of proof-of-principle of thermal insulation of banana peels with polystyrene were researched for their effectiveness for thermal retardancy. This research tested various different weight ratios of banana peels to polystyrene for their thermal conductivity, thermal stability, and structural integrity. It was found that thermal insulation abilities increase as the banana peel content increases, as reflected in the low total weight loss and high crystallinity percentages. It was suggested that the high lignin and cellulose content in the banana peel is the cause as they were the last ones to decompose per the structural integrity analysis. It was concluded that these prototypes with highest banana peel content can be effective enough to replace the commercial thermal insulators although further research was suggested for mechanical properties for industrial implementation (Mohamed et al., 2023). Although thermal insulation ability was proven effective, this study does not indicate the ripening stage of banana peels used or explored other chemical compositions of the banana peels such as other high char-forming chemical properties such as tannic acid. High lignin and cellulose contents was suggested to be a possible cause of the increase in thermal stability. However, lignin and cellulose contents differ in the ripening stages of banana peels. During the softening process of the ripening, cellulose decreases and lignin increases (View of COMPARATIVE STUDY on NUTRIENT COMPOSITION and FUNCTIONAL CHARACTERISTICS of TROPICAL FRUITS with EMPHASIS on BANANA FRUIT PEEL | International Journal of Pharmacy and Pharmaceutical Sciences, 2024). Therefore, it is inconclusive as to how ripening stages or different levels of chemical components in banana peels affect their inherent thermal properties.
Another approach to see how banana peel ripeness affects its thermal stability is to look at the mechanical properties. The extraction of cellulose from banana peels seemingly became effective methods as cellulose has strong mechanical properties with high molecular weights and a long chain of molecules (W. T. Wulandari et al 2016 IOP Conf. Ser.: Mater. Sci. Eng. 107 012045). For this reason, cellulose has been becoming a popular research area for bio-composites. A study conducted in 2021 tested composites made with banana fibers extracted from peels. The banana fibers were treated with NaOH 5% solution as an alkali treatment to remove lignin and hemicellulose. The composites were made with different weight ratio of treated banana fibers to epoxy resin for their mechanical and fire retardant properties. The study suggested that both properties plateaued at 20% banana fiber weight as the 25% testing group started to show a decline in mechanical strength and thermal properties (Banana Fiber-Reinforced Epoxy Composites: Mechanical Properties and Fire Retardancy – ProQuest, 2021). Although this study suggests the maximum benefit of mechanical and thermal properties of cellulose to be 20% banana fiber, it is unclear the ratio of cellulose in the 20% banana fiber. In addition, 20% banana fiber may have other chemical components that were not removed from the alkali treatment such as phosphorus.
The studies above and others do not mention the ripening stage of banana peels used in the research. Although the research has proposed the significance of thermal properties of banana peels and suggested lignin and cellulose may influence thermal properties, there remains a gap in the literature as decisive evidence of how the chemical changes or different levels of chemical composition in the banana peels affect their thermal properties. As the banana peels ripen, starch is turned into sugar such as sucrose, glucose, and fructose, resulting in higher sugar and lower starch contents in ripened banana peels (Hikal et al., 2022). Conversely, tannic acid content
decreases as banana peels ripen as tannic acids are bioactive compounds in the unripe banana peels to protect the fruit. During the softening process of the ripening, cellulose decreases and lignin increases. Studies have suggested higher phosphorus content in ripe banana peels as compared to the unripe banana peels (View of COMPARATIVE STUDY on NUTRIENT COMPOSITION and FUNCTIONAL CHARACTERISTICS of TROPICAL FRUITS with EMPHASIS on BANANA FRUIT PEEL | International Journal of Pharmacy and Pharmaceutical Sciences, 2024). Understanding these ripening effects to the thermal properties is critical as it can provide effective and efficient methods for processing banana peels for bio-composites which can assist in improving the integration of the circular economy. As such, this was the subject of my experiment, how ripening stages of banana peels affect the thermal properties.
To prove the thermal properties of materials, there are many areas to study such as physical properties, mechanical properties, thermal conductivity, and thermal stability (Bentz et al., 2005). However, proving thermal properties of banana peels was not the subject of my experiment. Instead, understanding how ripening stages of banana peels behave to resist heat can support the subject of my experiment. Thus, my experiment focused on thermal stability to test the materials’ ability to resist heat by measuring the change in mass when exposed to the controlled heat (Klaudia Król-Morkisz & Kinga Pielichowska, 2019). This led to the development of my leading question: Does ripening stages of banana peels significantly affect thermal stability? Using the experimental method by directly testing three major stages of banana peels, unripe, ripe, and overripe for their thermal stability was deemed the best method to respond to my research question. I hypothesized that ripening stages of banana peels significantly affect thermal stability and that the unripe stage of banana peel is best at providing thermal stability. As other research suggested, the cellulose may hold a key to increase thermal stability due to their strong mechanical properties. As noted earlier, as banana peels go through the softening stages, peels decrease their cellulose and increase their lignin content. Therefore, unripe banana peels have a higher content of cellulose as compared to ripe and overripe banana peels. Once the effect of ripening stages of thermal stability is identified, it can be used to identify the best approach to the industrial implementation for the bio-composite; thereby, improving the integration of the circular economy.
Methods
The research design was based on the experimental method using an instrument called thermogravimetric analyzer. This instrument has a plate embedded with a precision balance which is situated in the furnace with the capacity to control the continuous temperature increase and time. Weights are measured continuously as temperature increases throughout the time programmed (Ropp, 2004). At the end of the set program, the thermogravimetric analyzer produces thermograms with thermogravimetric (TGA) and derivative thermogravimetry curves (DTG). The TGA curve shows the change in the mass of testing groups as constant increases in temperatures and their derivatives or rate of change in mass as a function of temperature increase are reflected in the DTG curves. It is a common industrial process to quantitatively analyze data from TGA and DTG curves using descriptive statistical methods (Klaudia Król-Morkisz & Kinga Pielichowska, 2019). TGA in quantitative thermal analysis is widely accepted and used to evaluate thermal stability, as it shows changes in mass in temperature stresses. Not only do many research for thermal stability use thermogravimetric analyzers, American Society for Testing and Materials International has a safety standard called ASTM E 2550 to use thermogravimetric analyzers to ascertain the quality of material by analyzing the thermal stability (Standard Test Method for Thermal Stability by Thermogravimetry, 2021).
Material preparation
The independent variable was three ripening stages of banana peel powder which were unripe, ripe, and overripe. Three ripening stages were based on the appearance of the bananas. Unripe had green skin. Ripe had yellow with brown dots skin. Overripe had brown skin. Same procedures were followed to make the banana peel powders for each independent variable. Banana peels were cut into small sizes, approximately 1cm by 1cm, and put in a NESCO dehydrator for 12 hours. Using the blender, they were blended powder. Then they were all sieved through a fine double mesh strainer. All of the instruments were cleaned before preparing each banana peel powder. Thus, cross contamination among the variables should not have occurred. These powders were then mixed with the binder to make a polymer at the weight ratio of 20g of peel powder to 20g of epoxy resin. The binder used was NASUBI epoxy resin. There were three experimental groups, unripe banana peel and resin polymer, ripe banana peel and resin polymer, and overripe banana peel and resin polymer. The control was 20g epoxy resin only. The sizes of polymer tested for each experimental group was also kept the same. HistoCore Mulicut instrument was used to cut the polymers based on 50μm in thickness in 0.089μm increment to be tested in the thermogravimetric analyzer. Thus, the constant variables were weight ratio used for peels and resin (20g peel powder, 20g epoxy resin), same procedure was used to prepare the polymer and banana peel powder, and the size of polymer tested for each experimental group.


For my experiment, Waters 5500 thermogravimetric analyzer was used at B.Braun Medical Inc as noted in Picture 2. This thermogravimetric analyzer was programmed to run 10oC increase in temperature per minute to 600oC. As thermogravimetric analyzers are known to be sensitive to ambient conditions, each experimental group had three trials to ensure consistency and repeatability. These trials were held on different days to ensure that the ambient condition did not have a material effect. Data from all trials were compared to ensure the confidence level based on the standard deviation. This process was done prior to analyzing the data quantitatively. Thermograms data from TGA and DTG curves were used to conduct a quantitative analysis using the descriptive method to study the effect of ripening stages of banana peels to their thermal stability. Using the temperature range from the TGA curve, each degradation peak phase was assigned. The peak temperatures at each degradation phase were used to identify the thermal characteristics. The weight loss percentage and total remaining material percentage were used as dependent variables to measure the thermal stability performance.
Data Analysis
The thermogravimetric analyzer generated thermograms as it continuously measured the material’s weight simultaneously. Thermograms illustrate two curves, thermogravimetric (TGA) and derivative thermogravimetry (DTG) curves as shown in Figure 1. The TGA curve shows the change in the mass of testing groups as constant increases in temperatures by 10oC per minute to 600oC. Their derivatives or rate of change in mass as a function of temperature increase are reflected in the DTG curves. If the TGA curve identifies weight loss or gain, the DTG curve records the deviation as a negative or positive value, respectively. Accordingly, the DTG curve reflects zero changes if TGA does not detect any weight loss or gain. In my testing groups, weight gains, which would indicate oxidation or reaction with the atmosphere, were not detected. Significant weight loss percentages are reflected as peaks in degradation in the DTG curves. The temperature ranges of the peaks in degradation are reflected as slopes of the TGA curve. The remaining material percentage is reflected in the TGA curve at 600oC. Weight loss percentage and degradation peaks were transferred to excel spreadsheet from the DTG curves and the remaining material percentages and temperature ranges were transferred to excel spreadsheet from TGA curves.
The thermogravimetric analysis for each experimental group was run three times to ensure consistency and repeatability in the data, as TGA is sensitive to ambient conditions. For example, thermogravimetric analysis for unripe experimental groups were run three times in different testing days. For each experimental group, weight loss percentage, degradation peaks, temperature range, and remaining material percentage were transferred to excel and accessed for confidence in the data set by using the STDEV function in Excel. The result of the standard deviation ensured that data sets were consistent and ambient conditions did not materially affect the data results, because it indicates that all values are closer to the mean of all trials. Table 1 in the Result section details the result of standard deviation of all trials.
After the confidence level was obtained, it underwent data normalization. No data was eliminated. Instead of the number of the peaks in degradation, temperature ranges of the peaks in degradation in the DTG curves were used to assign each degradation phase. For example, the unripe banana peel group had a first degradation at the temperature range of 155ºC to 245ºC. Instead of assigning this to first degradation phase, it was assigned to second degradation phase as temperature ranges of other testing groups were similar to this range. The result of how the data normalization was applied to my data is discussed in the Result section.
After all the degradation peaks were normalized based on the similar temperature ranges for more accurate comparisons, TGA and DTG results were analyzed quantitatively using the descriptive method. Peak temperatures and weight loss percentage at each degradation phase were analyzed by comparing to the control group. Such analyses were then compared to the material remaining percentage to determine which banana peel group assisted the most in improving the thermal degradation. Degradation phases represent material mass change or thermal decompositions of chemical components in experimental groups. Thus, analyzing the peak temperature by the degradation phase depicts the characteristics of the thermal degradation of each group. By analyzing weight loss percentage in each degradation phase, it can provide how each thermal degradation characteristic contributes to the thermal decomposition rate of each banana peel group, because it can depict how each group improves or deteriorates the thermal degradation by peak phases. As mentioned, the temperature in the TGA was increased by 10oC per minute until 600oC. Thus, total remaining material percentages represent how much mass is still remaining in the experimental groups at 600oC after 60 minutes. Analyzing such a percentage can provide best-worst ranking of banana peel groups. Because the thermal degradation characteristics are addressed by each phase, the remaining material percentage is like a confirmation of how each banana peel group helped to improve the thermal degradation.
Therefore, by directly comparing quantitative weight loss percentages and peak temperatures in peak phases and total remaining material percentages, the methods directly answer my research question, does ripening stages of banana peels significantly affect thermal stability? The control only had epoxy resin and each experimental group had addition of banana peels in different ripening stages. Without other confounding factors between the control and experimental groups, my experiment is direct comparisons of the effect of ripening stages of banana peels. The significance of the effect can be addressed by the percentage differences or ranking among the experimental groups.
Results
Before quantitatively analyzing TGA data, the consistency of the results were evaluated with the STDEV function in Excel. As mentioned in the Data Analysis section, all experimental groups had three trial runs as TGA is sensitive to the ambient conditions. Table 1 shows that for all testing groups, 95% of the data were below 1 standard deviation of the mean. Thus, it was deemed that data sets were reliable and low variances are expected for all testing groups and surrounding conditions did not materially affect the data results.
Standard Deviation for 3 trial runs for all experimental groups | |||||||||||||
1st Degradation Phase | 2nd Degradation Phase | 3rd Degradation Phase | 4th Degradation Phase | ||||||||||
Weight loss % | Deg. peak temp | Temp Range | Weight loss % | Deg. peak temp | Temp Range | Weig ht loss % | Deg. peak temp | Temp Range | Weight loss % | Deg. peak temp | Temp Range | Total remai ning | |
Control | 0.26 | 0.05 | 0.82 | 0.00 | 0.00 | 0.00 | 0.34 | 0.44 | 0.23 | 0.98 | 0.15 | 0.29 | 0.64 |
Unripe | 0.00 | 0.00 | 0.00 | 0.82 | 0.07 | 0.26 | 0.57 | 0.49 | 0.62 | 0.36 | 0.23 | 0.07 | 0.51 |
Ripe | 0.39 | 0.72 | 0.28 | 0.03 | 0.41 | 0.37 | 0.62 | 0.25 | 0.38 | 0.77 | 0.46 | 0.95 | 0.59 |
Overrip e | 0.12 | 0.60 | 0.43 | 0.48 | 0.32 | 0.07 | 0.17 | 0.09 | 0.04 | 0.42 | 0.18 | 0.21 | 0.37 |
After the confidence level of the data was established, the values used for quantitative analysis from Figures 1-4 are shown in table 2. The wave curves in green (bottom curve) are DTG curves which are the derivatives of the TGA curve in blue (top curve that goes down). As a result of the data normalization, the unripe group was affected at the 1st-3rd degradation phases. The peak temperature at 295.23oC with the temperature range of 245ºC-325ºC was combined with the peak temperature at 266.81oC with the temperature range of 327ºC-425ºC for the 3rd degradation phase. The initial degradation phase at the temperature range of 155ºC to 245ºC was assigned as the second degradation phase instead of the first. The control group has no second degradation phase. These were deemed more accurate for the quantitative analysis as other experimental groups were in similar temperature ranges.






Table 2: The table represents a data summary from the thermograms from figure 1-4. All of the data points are from TGA and DTG curves.
For the first and second degradation phases of the control group, the temperature range for the first degradation phase was 60oC to 220oC which overlaps to other experimental groups’ second phase as shown in Table 2. If data normalization was applied, it wouldn’t reflect ripe and overripe data accurately, as they experienced distinct first and second peak degradation phases. Thus, it was deemed that quantitative analysis can be done by first and second phases in a unified manner for weight loss percentage analysis to identify the rate of improvement in thermal degradation and in an individual manner for peak temperature analysis to identify the thermal degradation characteristics.
In the first and second degradation phases, control and unripe groups had a single phase while ripe and overripe groups had two distinct degradation phases. Control had a degradation peak at 126.53ºC in the temperature range of 60ºC-220ºC with total weight loss percentage of 16.38% while unripe group had a peak at 213.4oC in the temperature range of 155ºC-213.4ºC with total weight loss percentage of 11.85%. Thus the unripe experimental group was able to delay the degradation peak temperature and produce less weight loss percentage. As noted in Table 3, unripe produced 4.53% less weight loss percentage than the control.
1st degradation | 2nd degradation | 3rd degradation | 4th degradation | |
Unripe | -4.53% | -5.41% | -0.13% | |
Ripe | 2.22% | -16.58% | 9.42% | |
Overripe | -4.30% | -28.99% | -3.38% |
As stated prior, the ripe group had a similar degradation characteristic of two distinct degradation phases to the overripe group, with peaks below 100oC and 201oC in the first and second degradation phases. In spite of the similar characteristics, the ripe group had produced 2.22% more weight loss percentage as compared to the control while the overripe group produced 4.3% less weight loss percentage than control as noted in Table 3. Conversely, while unripe and overripe had different degradation characteristics, they had similar weight loss percentage improvements at 4.53% and 4.30%, respectively.
The third peak degradation phase had the most weight loss percentage as compared to other phases for all experimental groups. All banana peel experimental groups had lower peak temperatures than the control group. Moreover, all the experimental groups with banana peels improved the weight loss percentage as compared to the control group as noted in Table 3. Overripe group improved the most by 28.99%, followed by ripe and unripe by 16.58% and 5.41%, respectively. During the fourth peak degradation, all banana peel experimental groups had lower peak temperatures than the control group. However, the ripe group was the only experimental group that produced more weight loss percentage while all other banana peel experimental groups were able to reduce the weight loss percentages. The overripe group was able to improve the weight loss percentage the most by 3.38% compared to the control. Unripe group had a slight weight loss percentage improvement by 0.13% compared to the control. However, ripe increased the weight loss percentage by 9.42% compared to the control. A bar graph was generated to clearly show the effects of weight loss percentage in Figure 5.


As shown in Figure 5, the overripe experimental group was able to assist the most in reducing the weight loss percentage throughout the peak degradation phases. Especially during the third degradation period by approximately 30% as compared to the control. As noted in Figure 6, overripe had a significant improvement with a 36% increase in total remaining material percentage. The second best experimental group that assisted in a reduction of weight loss percentage was the unripe group. Although the unripe group was able to help in reduction of weight loss percentage throughout the peak phases, it was more helpful until the third phase which ranged until 425oC. As noted in Figure 6, there was a slight improvement in the total remaining material percentage by 5%. The least beneficial group was the ripe group. It was only able to assist in reduction of weight loss percentage during the third peak degradation by approximately 17%. It produced more weight loss percentages in other degradation peak phases as compared to the control. As noted in Figure 6, the ripe group had an increase in total remaining material percentage by 2% which was the least helpful among other banana peel groups.
Discussion
The experimental groups exhibited distinct degradation behaviors, revealing noteworthy differences between ripe, overripe, unripe, and control samples. Ripe and overripe groups displayed two distinct peaks in their 1st and 2nd degradation profiles, whereas control and unripe groups demonstrated a single peak. This disparity suggests that the chemical composition of ripe and overripe banana peels may undergo decomposition in multiple stages, potentially involving various chemical components.
In the initial phase of degradation, temperatures ranging from 70°C to 150°C, the breakdown of sugars, particularly fructose, is likely to occur. Fructose typically decomposes around 140°C, aligning with the temperature range of the first degradation phase (J. NOLASCO JR & Massaguer, 2006). Subsequently, in the second degradation phase spanning temperatures from 150°C to 250°C, multiple chemical components, including carbohydrates, hemicellulose, glucose, and sucrose, may decompose. Carbohydrates decompose from 164°C to 497°C (Wei Hsin Chen et al., 2018), hemicellulose at 220°C (Yang et al., 2007), glucose between 188°C to 220°C (Kang & Zhang, 2020), and sucrose at 186°C (Šimkovic et al., 2003). The distinct presence of two degradation peaks in ripe and overripe groups can be attributed to the breakdown of these chemical components across different temperature ranges.
Quantitative analysis during the first and second degradation phases revealed similar improvements in weight loss percentage for unripe and overripe groups, despite different degradation characteristics, standing at 4.53% and 4.3%, respectively. In contrast, ripe samples exhibited a notable increase in weight loss percentage by 2.22%, even though they shared similar degradation characteristics with overripe groups. Additionally, the unripe group demonstrated a delay in peak temperature compared to the control group during these phases. These findings suggest that the chemical composition of unripe and overripe peels may offer better protection against degradation compared to ripe peels. Unripe banana peels are higher in carbohydrates and cellulose than ripe banana peels which could assist in protecting the mass from degradation for the unripe group. As carbohydrate turns into sugar components as it ripens, the sugar components increase in ripe to overripe peels. Similarly, during the softening stages of the ripening process, cellulose components decrease while lignin increases. Ripe banana peels have lower carbohydrates and cellulose than unripe banana peels and also ripe banana peels have lower sugar components than overripe banana peels. Such chemical component differences may have caused the ripe group to have an adverse effect of increasing the weight loss percentage while unripe and overripe groups improve the weight loss percentage in the first and second peak phases.
The third peak degradation phase exhibited the highest weight loss percentage across all experimental groups, indicating substantial chemical breakdown compared to other temperature ranges. Components such as tannic acid (decompose at 350oC) (Xia et al., 2015), cellulose (decompose at 315oC) (Yang et al., 2007), phosphorus (decomposes at 250oC to 310oC) (Howell & Daniel, 2015), and lignin (decompose at 280oC to 350oC; max at 450oC to 500oC) (Nassar & MacKay, 2024) likely contribute to this phase. Despite exhibiting lower peak temperatures than the control, all banana peel experimental groups managed to reduce weight loss percentage. This suggests that certain chemical components may undergo degradation at lower temperatures while still protecting the remaining mass, resembling intumescent characteristics, where decomposed materials act as insulation layers, slowing down heat transfer through char (Bhat, 2013).
In the fourth peak degradation phase, only the ripe group demonstrated an increase in weight loss percentage, although all experimental groups exhibited similar degradation characteristics with lower peak temperatures than the control. The unripe group was able to decrease weight loss percentage very minorly, with a slight improvement of 0.13%. However, the overripe group showed significant protection against heat transfer, indicating the presence of chemical components that delay heat transfer effectively, similar to intumescent characteristics.
Throughout the degradation phases, each experimental group exhibited intumescent-like characteristics, with the overripe group providing the most significant protection against heat transfer. It provided a consistent and stable degradation throughout the phases. Its effectiveness is also evident in the total material remaining percentage as it significantly improved it by 36% compared to the control. The unripe group was effectively able to protect the mass from heat transfer until the third phase until approximately 425oC. Beyond this temperature, it can only slightly improve the thermal degradation as evident in the fourth degradation phase and remaining material percentage of 8% which is 5% higher than the control group. Ripe group was least effective among other experimental groups in protecting the mass from heat transfer. It was only effective in the third degradation phase at the temperature range of 240oC-370oC. The material remaining percentage at 600oC was 5% which was a slight improvement of 2% as compared to the control.
Therefore, a conclusion can be reached that the ripening stages of banana peels can make degrees of difference to thermal degradation. I accept my hypothesis that ripening stages of banana peels significantly affect thermal stability. However, I rejected my hypothesis that the unripe stage of banana peel is best at providing thermal stability. The findings show evidence that adding the unripe and ripe banana peels can slightly improve the overall thermal degradation; however, using the overripe banana can improve overall thermal degradation substantially more than other ripening stages tested. These findings suggest that there are chemical components in the overripe banana peels that may delay the heat transfer more effectively than the chemical components that are dominant in unripe or ripe peels. Because cellulose is higher in unripe than overripe banana peels, the mechanical strength of the cellulose may not be as effective in thermal stability as some chemical components in the overripe banana peels. Identifying such chemical components was beyond the scope of my paper, which are discussed in the Future Study and Limitation section in this paper. However, such conclusive evidence that overripe stages may significantly influence the thermal stability of the bio-polymers answers my research question. Knowing this, it’s a direct response to my project goal to determine if the effects of the ripening stages of banana peels is significant to the thermal properties as it can help identify the best approach to repurpose the banana peel wastes. Researchers in the field can consider the effect of the ripening stages of banana peels used in the bio-composite to determine the most effective stages of banana peels to use in their research. As many different ripening stages of banana peels wastes are created throughout the supply chain, creating bio-polymers using banana peels with the need for certain ripening stages of banana peels, would be critical to improve the circular economy.
Limitations
Although the thermogravimetric analysis used in my research addresses the thermal degradation characteristics, it cannot identify what chemical components were decomposed at each peak degradation phase or remained at the end of the experiment. To identify such chemical components, chemical testing or TGA-Mass Spectrometry analysis should be conducted. Not knowing the exact chemical component that decomposed did not influence the result of my experiments as my research question and goal were not based on answering why the ripening stages of banana peels significantly affect their thermal stability. Rather, it was to determine the conclusive evidence of ripening stages of banana peels’ significant effects on thermal stability. Degradation characteristics were identified in my research so that it can help to determine the effects of the weight loss percentage and total remaining material percentage. As such, certain chemical components were identified as possibilities that are creating intumescent-like behavior to protect the remaining material from the heat transfer. These were based on the research literatures and are consistent with other research; however, determining the exact chemical components that decomposed at each degradation phase and remaining at the end of the experiments can establish a direct cause-and-effect relationship. For instance, if the exact chemical components were identified, they can help establish the cause-and-effect relationships of decomposed chemical materials at each degradation phase and how such degradation affected the remaining chemical materials, rather than simply identifying the thermal stability characteristics. Knowing this, it can further help the research in this field as we can isolate the chemical components or combination that caused the improvement in thermal stability.
Future Research
In the continuation of this research, I plan to use the mass spectrometry to identify the chemical components that decomposed and remained at the end of the experiment to establish the cause-and-effect relationship. TGA-MS analysis can be conducted with the TGA by using a mass spectrometer. The mass spectrometer is an attachment to the TGA and when the TGA identifies peaks in the mass loss, it ionizes the compounds and sends the information into the mass spectrometer to identify the chemical components decomposed (Thermogravimetric Analysis – Mass Spectroscopy (TGA – MS), 2022). By being able to identify the specific chemical components being decomposed, it would then be able to conclusively determine what chemical components are responsible for aiding in protecting the remaining materials in the sample. The goal of such future research would then be to answer the question why the ripening stages of the banana peels significantly affect their thermal stability?
Bibliography
- 2023: A historic year of U.S. billion-dollar weather and climate disasters. (2023). NOAA Climate.gov. https://www.climate.gov/news-features/blogs/beyond-data/2023-historic-year-us-billion-d ollar-weather-and-climate-disasters
- Antonella Violano, & Cannaviello, M. (2023). The Carbon Footprint of Thermal Insulation: The Added Value of Circular Models Using Recycled Textile Waste. Energies (Basel), 16(19), 6768–6768. https://doi.org/10.3390/en16196768
- Banana Fiber-Reinforced Epoxy Composites: Mechanical Properties and Fire Retardancy – ProQuest. (2021). Proquest.com. https://www.proquest.com/openview/20cc24ca2b83589895a7ae5ee7b13a23/1?pq-origsite =gscholar&cbl=237276
- Bananas: production volume worldwide 2022 | Statista. (2022). Statista; Statista. https://www.statista.com/statistics/716037/global-banana-market-volume/#:~:text=This% 20statistic%20shows%20the%20production,been%20generally%20increasing%20since% 202010
- Basic Information about Landfill Gas | US EPA. (2016, April 15). US EPA. https://www.epa.gov/lmop/basic-information-about-landfill-gas
- Bentz, D. P., Prasad, K. R., & Yang, J. C. (2006). Towards a methodology for the characterization of fire resistive materials with respect to thermal performance models. Fire and Materials, 30(4), 311–321. https://doi.org/10.1002/fam.916
- Bhat, G. S. (2013). Flame resistant nonwoven fabrics. Elsevier EBooks, 322–348. https://doi.org/10.1533/9780857098931.2.322
- CGR 2021. (2021). Circularity-Gap.world. https://www.circularity-gap.world/2021
- Cheng, G., Duan, X., Yang, B., Jiang, Y., Lu, W., Luo, Y., & Jiang, W. (2007). Effect of hydroxyl radical on the scission of cellular wall polysaccharides in vitro of banana fruit at various ripening stages. Acta Physiologiae Plantarum/Acta Physiologiae Plantarum, 30(2), 257–263. https://doi.org/10.1007/s11738-007-0116-4
- Chollet, B., José-Marie Lopez-Cuesta, Fouad Laoutid, & Ferry, L. (2019). Lignin Nanoparticles as A Promising Way for Enhancing Lignin Flame Retardant Effect in Polylactide. Materials, 12(13), 2132–2132. https://doi.org/10.3390/ma12132132
- Food Waste and its Links to Greenhouse Gases and Climate Change. (2024). Usda.gov. https://www.usda.gov/media/blog/2022/01/24/food-waste-and-its-links-greenhouse-gases -and-climate-change
- Hikal, W. M., Hussein, Amra Bratovcic, Tkachenko, K. G., Javad Sharifi-Rad, Miroslava Kačániová, Elhourri, M., & Atanassova, M. (2022). Banana Peels: A Waste Treasure for Human Being. Evidence-Based Complementary and Alternative Medicine (Print), 2022, 1–9. https://doi.org/10.1155/2022/7616452
- Howell, B. A., & Daniel, Y. G. (2015). Thermal degradation of phosphorus esters derived from isosorbide and 10-undecenoic acid. Journal of Thermal Analysis and Calorimetry, 121(1), 411–419. https://doi.org/10.1007/s10973-015-4487-2
- Hwong, A. R., Wang, M., Khan, H., D Nyasha Chagwedera, Grzenda, A., Doty, B., Benton, T., Alpert, J., Clarke, D., & Compton, W. M. (2022). Climate change and mental health research methods, gaps, and priorities: a scoping review. the Lancet. Planetary Health, 6(3), e281–e291. https://doi.org/10.1016/s2542-5196(22)00012-2
- J. NOLASCO JR, & Massaguer, P. R. (2006, September 20). Thermal degradation kinetics of sucrose, glucose and fructose in sugarcane must for bioethanol production. ResearchGate; Wiley. https://www.researchgate.net/publication/229871366_Thermal_degradation_kinetics_of_ sucrose_glucose_and_fructose_in_sugarcane_must_for_bioethanol_production
- Kang, W., & Zhang, Z. (2020). Selective Production of Acetic Acid via Catalytic Fast Pyrolysis of Hexoses over Potassium Salts. Catalysts, 10(5), 502–502. https://doi.org/10.3390/catal10050502
- Klaudia Król-Morkisz, & Kinga Pielichowska. (2019). Thermal Decomposition of Polymer Nanocomposites With Functionalized Nanoparticles. Elsevier EBooks, 405–435. https://doi.org/10.1016/b978-0-12-814064-2.00013-5
- Liu, W., Chen, D.-Q., Wang, Y.-Z., Wang, D.-Y., & Qu, M.-H. (2007). Char-forming mechanism of a novel polymeric flame retardant with char agent. Polymer Degradation and Stability, 92(6), 1046–1052. https://doi.org/10.1016/j.polymdegradstab.2007.02.009
- Mohamed, G. R., Mahmoud, R. K., Shaban, M., Fahim, I. S., H. M. Abd El‐Salam, & Mahmoud, H. M. (2023). Towards a circular economy: valorization of banana peels by developing bio-composites thermal insulators. Scientific Reports (Nature Publishing Group), 13(1). https://doi.org/10.1038/s41598-023-37994-1
- Nassar, M. M., & MacKay, M. (2024). Mechanism of Thermal Decomposition of Lignin. Wood and Fiber Science, 441–453. https://wfs.swst.org/index.php/wfs/article/view/262
- New Analysis of National Climate Plans: Insufficient Progress Made, COP28 Must Set Stage for Immediate Action | UNFCCC. (2020). Unfccc.int. https://unfccc.int/news/new-analysis-of-national-climate-plans-insufficient-progress-mad e-cop28-must-set-stage-for-immediate#:~:text=UN%20Climate%20Change%20News%2 C%2014,goals%20of%20the%20Paris%20Agreement
- Price, E. J., Covello, J., Paul, R., & Wnek, G. E. (2021). Tannic acid based super‐intumescent coatings for prolonged fire protection of cardboard and wood. SPE Polymers, 2(2), 153–168. https://doi.org/10.1002/pls2.10043
- Provisional State of the Global Climate 2023. (2023). World Meteorological Organization. https://wmo.int/files/provisional-state-of-global-climate-2023
- Punongbayan, A. M., Austria, E. E., Hemedez, A. M., Romero, G. C., Jay, A., Vanguardia, S. C., Agustin, E. V., Salazar, E. C., Sugpatan, J., & Ian, J. (2021). Utilization of Banana Peel and Carton Waste in Manufacturing of Thermal Insulation Board. 2021 IEEE 13th International Conference on Humanoid, Nanotechnology, Information Technology, Communication and Control, Environment, and Management (HNICEM). https://doi.org/10.1109/hnicem54116.2021.9731942
- Ropp, R. C. (2004). The Solid State: Mechanisms of Nucleation, Solid State Diffusion, Growth of Particles and Measurement of Solid State Reactions. Studies in Inorganic Chemistry, 113–218. https://doi.org/10.1016/s0169-3158(04)80006-9
- Šimkovic, I., Igor Šurina, & Marek Vričan. (2003). Primary reactions of sucrose thermal degradation. Journal of Analytical and Applied Pyrolysis (Print), 70(2), 493–504. https://doi.org/10.1016/s0165-2370(03)00007-x
- Standard Test Method for Thermal Stability by Thermogravimetry. (2021). Astm.org. https://www.astm.org/e2550-21.html
- Sugar and salts create sponge for capturing carbon dioxide – Materials Today. (2022, November 30). Materials Today. https://www.materialstoday.com/materials-chemistry/news/sugar-salts-create-sponge-carb on-dioxide/
- Thermogravimetric Analysis – Mass Spectroscopy (TGA – MS). (2022). KU Leuven Institute for Micro- and Nanoscale Integration. https://limni.kuleuven.be/expertise-facilities/analytical-techniques/Thermogravimetric-A nalysis-Mass-Spectroscopy-%28TGA-MS%29
- Types of Extinguishers | Ohio University. (2024). Ohio.edu. https://www.ohio.edu/facilities/safety/fire/extinguisher/types
- US. (2020, February 6). Majority of US Adults Believe Climate Change Is Most Important Issue Today. Https://Www.apa.org. https://www.apa.org/news/press/releases/2020/02/climate-change
- USDA ERS – Food Loss: Why Food Stays On the Farm or Off the Market. (2017). Usda.gov. https://www.ers.usda.gov/amber-waves/2020/march/food-loss-why-food-stays-on-the-far m-or-off-the-market/#:~:text=Through%20the%20entire%20supply%20chain,distribution %2C%20and%2042%20percent%20at
- View of COMPARATIVE STUDY ON NUTRIENT COMPOSITION AND FUNCTIONAL CHARACTERISTICS OF TROPICAL FRUITS WITH EMPHASIS ON BANANA FRUIT PEEL | International Journal of Pharmacy and Pharmaceutical Sciences. (2024). Innovareacademics.in. https://journals.innovareacademics.in/index.php/ijpps/article/view/44144/26382
- Wei Hsin Chen, Yen Shih Chu, Jenn Long Liu, & Jo Shu Chang. (2018). Thermal degradation of carbohydrates, proteins and lipids in microalgae analyzed by evolutionary computation. Energy Conversion and Management, 160, 209–219. https://doi.org/10.1016/j.enconman.2018.01.036
- Wulandari, W. T. “Nanocellulose Prepared by Acid Hydrolysis of Isolated Cellulose from Sugarcane Bagasse.” Iopscience.iop.org, IOP Publishing, 2016, iopscience.iop.org/article/10.1088/1757-899X/107/1/012045/pdf#:~:text=Nanocellulose %20has%20a%20higher%20surface,2%2C3%2C5%5D. Accessed 6 Apr. 2024.
- Xia, Z., Singh, A., Weeradech Kiratitanavit, Ravi Mosurkal, Kumar, J., & Nagarajan, R. (2015). Unraveling the mechanism of thermal and thermo-oxidative degradation of tannic acid. Thermochimica Acta, 605, 77–85. https://doi.org/10.1016/j.tca.2015.02.016
- Yang, H., Yan, R., Chen, H., Dong Ho Lee, & Zheng, C. (2007). Characteristics of hemicellulose, cellulose and lignin pyrolysis. Fuel, 86(12-13), 1781–1788. https://doi.org/10.1016/j.fuel.2006.12.013
About the author
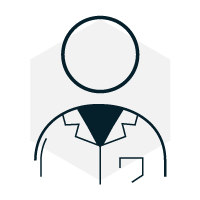
Preston Wang
Preston is a rising senior at Tesoro High School. He has participated and placed in the California Science and Engineering Fair and Orange County Science and Engineering Fair throughout middle school, which fostered his desire to help people through scientific research and discovery. In high school, he began directly helping those in need at Mercy Warehouse, a nonprofit organization that works to provide impoverished families with necessities and he started a community health nonprofit organization, Unified Mind, focused on increasing positive emotions among children through extracurricular activities to support and improve mental health. In his spare time, Preston enjoys playing volleyball at his school and local clubs.
Preston’s overarching goal in life is to aid in preventing depression among the youth by focusing on the significance of building positive productive habits to maintain a positive outlook on life, and fulfill their full potential to reach their happiest self. To ameliorate the mental health crisis among the youth, he strives to create and promote positive outlets and environments for young individuals to ensure their long-term health and happiness with a solid state of well-being so that they can fight any adversity in life.